U.S. factory efficiency picked a fine time to stall.
The availability of skilled workers remains a roadblock, as ever-shifting trade policies accelerate the tide of reshoring—all while labor markets remain out of sync. Factories need to be fixed now.
With a shortage of workers and an estimated 402,000 open manufacturing jobs in the U.S., it’s clear that hiring alone won’t close the gap. Unlocking the full capabilities of the current workforce is the fastest and most sustainable solution.
While many manufacturers focus on long-term investments, there is an immediate opportunity to unlock the potential of the existing (and hard-to-find) workforce through improved planning, skill development, and AI-enabled optimization.
Forward-looking manufacturers can address many of the challenges posed by shifting demand and supply chain patterns directly on the shop floor. Well-designed labor optimization plans can build a more resilient workforce and increase output using existing resources.
The hidden factory in the factory
AlixPartners’ recent engagements at manufacturing plants across a variety of industries revealed a recurring problem: the current workforce is not being fully leveraged.
Clear gaps in skill sets, work allocation, and cross-training have led to stagnant performance, limited flexibility, and missed opportunities. Limited leadership presence on the floor and often unclear responsibilities reflect a lack of standard planning and contribute to persistent firefighting. Fixing the factory not only frees up machine time but also unlocks labor potential and capacity—without adding headcount or investing in additional capital equipment.
A sample study of one production line found that only 46% of time on a 12-hour shift was spent on value-added activities. With some rethinking of roles and training, the line could meet full production requirements with just 5–6 operators, rather than the 9 originally allocated. That extra labor can be used to hedge against absenteeism or to backfill open roles.
This isn’t an isolated case. Many manufacturers are operating with more people than ever before—and still falling short of performance targets. The solution isn’t more labor. It’s unlocking the labor already in place.
Five smart strategies to add to the productivity playbook
AlixPartners has developed five high-impact strategies that leaders can immediately implement to unlock capacity gains, improve efficiency, and strengthen workforce resilience.
1. Assess & analyze—find the gaps
Conduct a skills assessment and perform time studies to gain clear visibility into how work is performed, where time is lost, and how well employee capabilities match operational needs. Root-cause analysis will pinpoint the sources of inefficiency, such as excessive walking, searching for tools, or unclear instructions.
Translate time study findings and root cause analysis into actionable priorities for process redesign, workforce development, and role alignment. Use these insights to highlight training gaps, underused talent, and opportunities to redeploy staff where they add the most value. A clear baseline sets the stage for smarter decisions, better labor planning, and targeted improvements that drive productivity.
2. Clean-sheet the process—optimize workflow
The concept of “one man, one machine” is antiquated. Skill specialization is still important, but it’s one piece of the new puzzle. After root causing for value-added and non-value-added time and activities, go beyond just removing paperwork and steps to a workstation. Truly rethink how the work is grouped and done, as much as by whom.
Combining people to work in teams across modules or process steps is helpful in broadening employee skills and understanding of the full process. However, care must be taken to ensure that one person is not always assigned to or executing the same portion.
3. Capture knowledge and improve access—retain expertise
Document essential tribal knowledge from experienced workers into clear standard operating procedures, troubleshooting checklists, and best practice guides. This ensures that expertise stays within the company and reduces variability between shifts. Start where the biggest gaps are in needs.
Support this knowledge transfer with role-specific learning tools like microlearning modules, job shadowing, and on-demand resources (e.g., converting legacy knowledge into step-by-step digital work instructions with video and AI tools). These tools shorten onboarding times, reinforce safety, and help employees grow into new roles, creating a pipeline for internal advancement.
4. Develop and cross-train—build modern flexibility
Design and implement a focused cross-training plan based on the skills gaps and operational priorities identified during the initial assessment and aligned with the redesigned process. A well-rounded, cross-trained workforce can adapt quickly to shifting production needs and minimize downtime caused by absences.
Align scheduling practices with real production demands by adding flexible shifts, setting clear expectations, and offering attendance incentives. This reduces absenteeism, boosts morale, and helps retain skilled employees who value growth and stability.
Use AI-powered platforms to analyze workforce data, track certifications, and recommend personalized training paths while equipping employees with mobile apps, wearables, and digital SOP systems to streamline tasks and workflows. Accessible tools like kiosks and tablets keep the workforce engaged, attract next-generation talent, and provide real-time feedback to continuously improve floor operations.
5. Lead and coach proactively—maximize supervision
Establish daily, weekly, and monthly leadership routines through Leader Standard Work (LSW) to ensure proactive supervision, clear accountability, and hands-on problem-solving. Strong routines help supervisors stay focused on high-impact tasks instead of firefighting day-to-day issues.
For leaders burdened by too many meetings or low-value tasks, consider managerial deselection to remove or delegate less critical work. This frees up time to coach employees, reinforce safety and quality standards, and maintain a consistent floor presence that strengthens culture and performance.
Scale with the same headcount, but better practices
Meeting rising demand isn’t just about adding headcount—it’s about maximizing the value of the existing team. By boosting productivity and building workforce agility, organizations can scale efficiently without relying on new hires or additional applications.
To explore factory floor labor optimization in more detail, explore the links in the factory floor series below:
- Lessons from the factory floor part 1: These labor pains aren’t temporary
- Lessons from the factory floor part 2: The music has stopped on salaried churn. Now what?
- Lessons from the factory floor part 3: So many wrenches, so few wrench turners
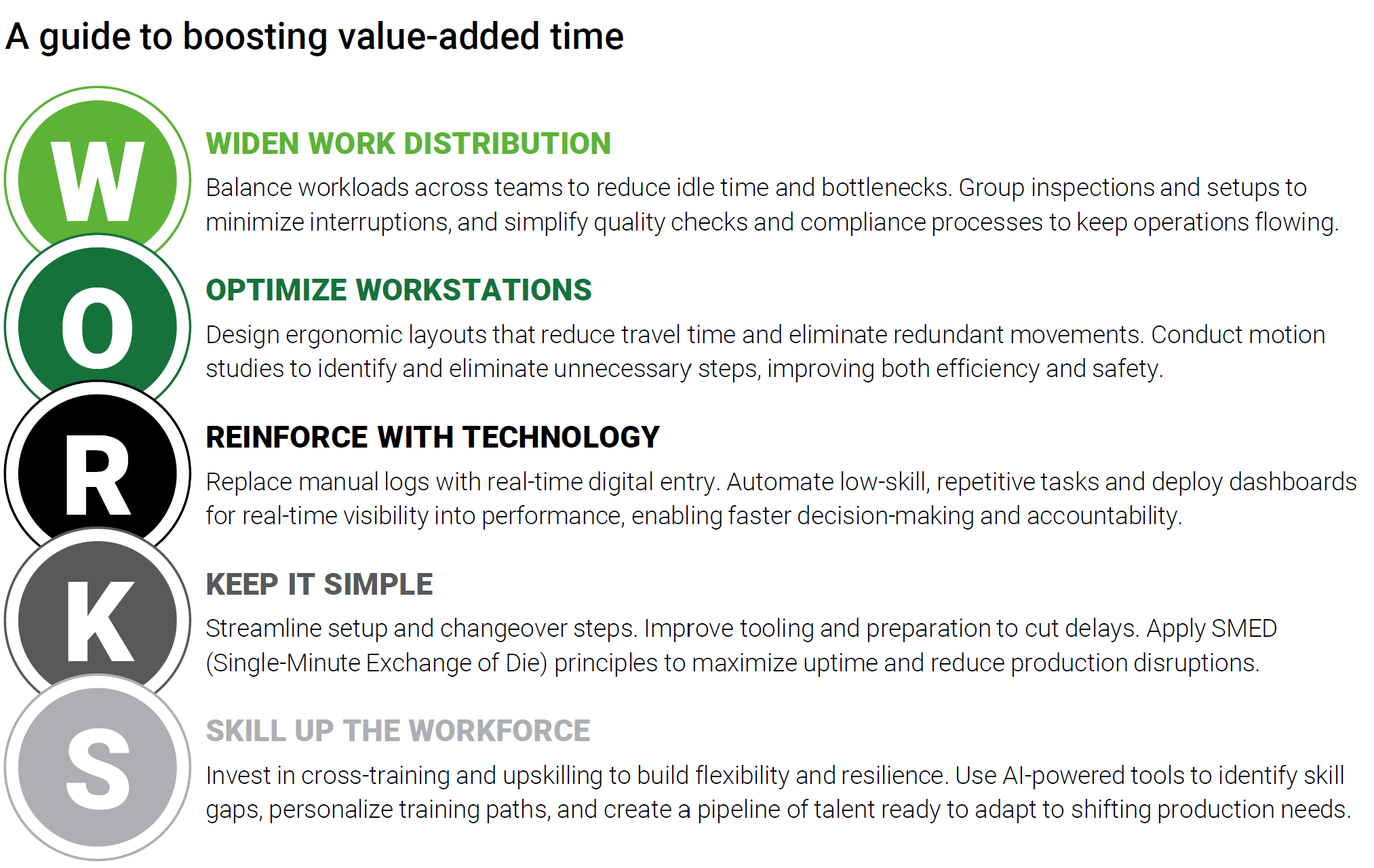