ESG imperative drives industry's future competitiveness – fully understanding the risks, opportunities, and responsibility is crucial for business.
The U.N. Climate Change Conference recently concluded with mixed results. Negotiators addressed hazards already plaguing the environment but made little progress on cutting future emissions. COP 27's difficulty generating specific solutions to the planet's long list of problems should embolden the global business community's ESG-driven calls for clearer regulation, industry collaborations, individual business targets, and actionable strategies. Time is not on anyone’s side.
The aviation industry's approach to ESG must likewise accelerate and broaden, going beyond cutting CO2 emissions of sold products, to address the entirety of the challenge. ESG is no longer a "soft" issue, and addressing it is not just a philanthropic effort, but a business imperative as well.
Aviation players – often singled out as disproportionately responsible for global emissions – need to craft ESG and sustainability strategies that indeed consider the environment, but also tackle the social and governance challenges that represent serious hurdles to future competitiveness and financial health.
Deriving such a holistic approach requires taking a broader view on ESG and sustainability. This is followed by analyzing the regulatory and financial drivers to understand impact, risks, and opportunities for the business.
UNDERSTANDING SUSTAINABILITY & ESGSustainability and ESG are often used synonymously and narrowly interpreted as emissions reduction from a general point of view – however the concepts are slightly different and much broader than just environmental concerns Sustainability – addressing the global perspective
ESG – addressing the business perspective
|
PURSUING A BROADER SET OF STRATEGIES
As it stands, the aviation industry is addressing the sustainability challenge (and setting net-zero targets for 2050) mainly from the viewpoint of environmental tolls rendered by greenhouse gas emissions of downstream activities in the value chain (namely CO2 emissions of aircraft operations – see Figure 1). This is obviously the first and most important avenue to make aviation sustainable. Recent figures disclosed by Airbus underscore this, indicating that 2021 value chain CO2 equivalent emissions related to Scope 3 "use of sold products" reflect 98% of total emissions, compared to 2% for Scope 1, 2, and 3 "purchased goods and services."
However, the issue needs to be tackled end-to-end because sustainability is defined as more than just CO2 (see definition box). Aerospace companies should review their individual climate impact and carbon footprint as well as compliance to social and governance standards within their own production perimeter, but not stop there. Analysis of downstream and upstream supply chain is necessary. ESG cannot be selectively applied.
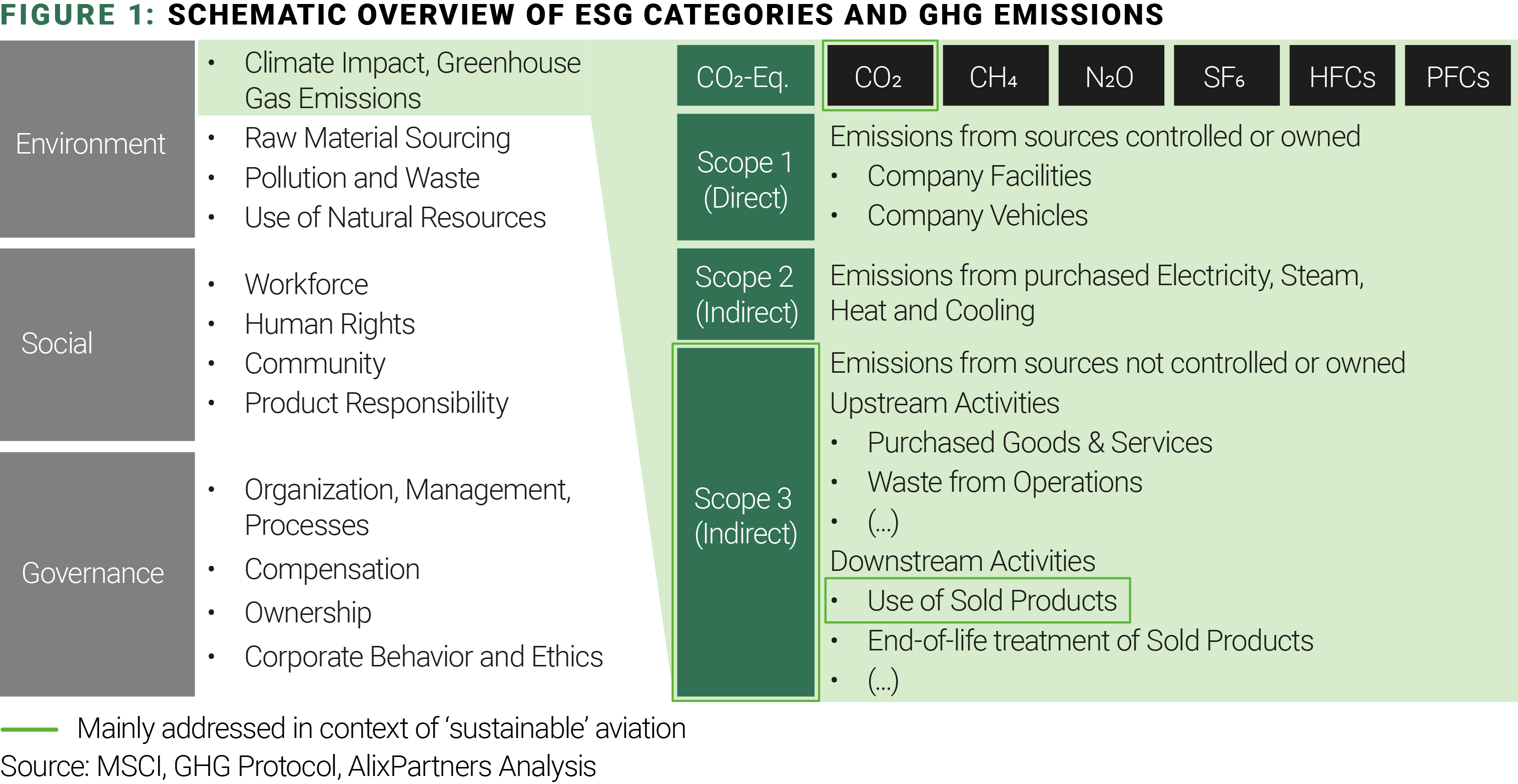
COUNTING THE IMPLICATION OF REGULATION AND THE COST OF INACTION
The European Union established a regulatory framework with reporting directives a half-decade ago, and updates are now being introduced with the EU Taxonomy and the Corporate Sustainability Reporting Directive (CSRD). The new regulation will be implemented stepwise, expanding reporting requirements to ESG aspects, and addressing five-times the number of companies addressed today.
In the U.S., the Securities and Exchange Commission (SEC) is following close behind. Its recent proposal seeks to enhance and standardize disclosures related to ESG factors considered by funds and advisors, as well as require public companies to disclose extensive climate-related information in filings.
Carbon pricing mechanisms will greatly influence the cost of carbon emissions. There are 68 carbon pricing systems in place as of 2022, compared to just two in 1990, according to the World Bank. The absolute price and the social cost of carbon will only rise, becoming an expense for both for production and use of airplanes. Similar mechanisms will likely follow for other areas in the ESG framework. Ignoring this reality will directly hit the bottom line.
The European Commission adopted in mid-2021 a series of legislative proposals (Fit for 55) setting out how it intends to achieve climate neutrality in the EU. This included the intermediate target of at least 55% net reduction in greenhouse gas emissions by 2030 (61% for sectors covered by the EU Emissions Trading System (ETS)).
The overall volume of greenhouse gases that can be emitted by power plants, industry factories, and the aviation sector covered by the EU ETS is limited by an emission allowances 'cap' – one emission entitles the right of emitting one ton of CO2. Within the cap, companies receive or buy emission allowances that they can trade as needed. The cap decreases every year, ensuring total emissions fall.
Figure 2 shows the evolution of the cost of carbon in the ETS since 2012 when Intra-European Aviation was placed under the EU ETS umbrella; the potential future development; and the price level of 130 EUR per allowance that would be required to achieve this 61% reduction.
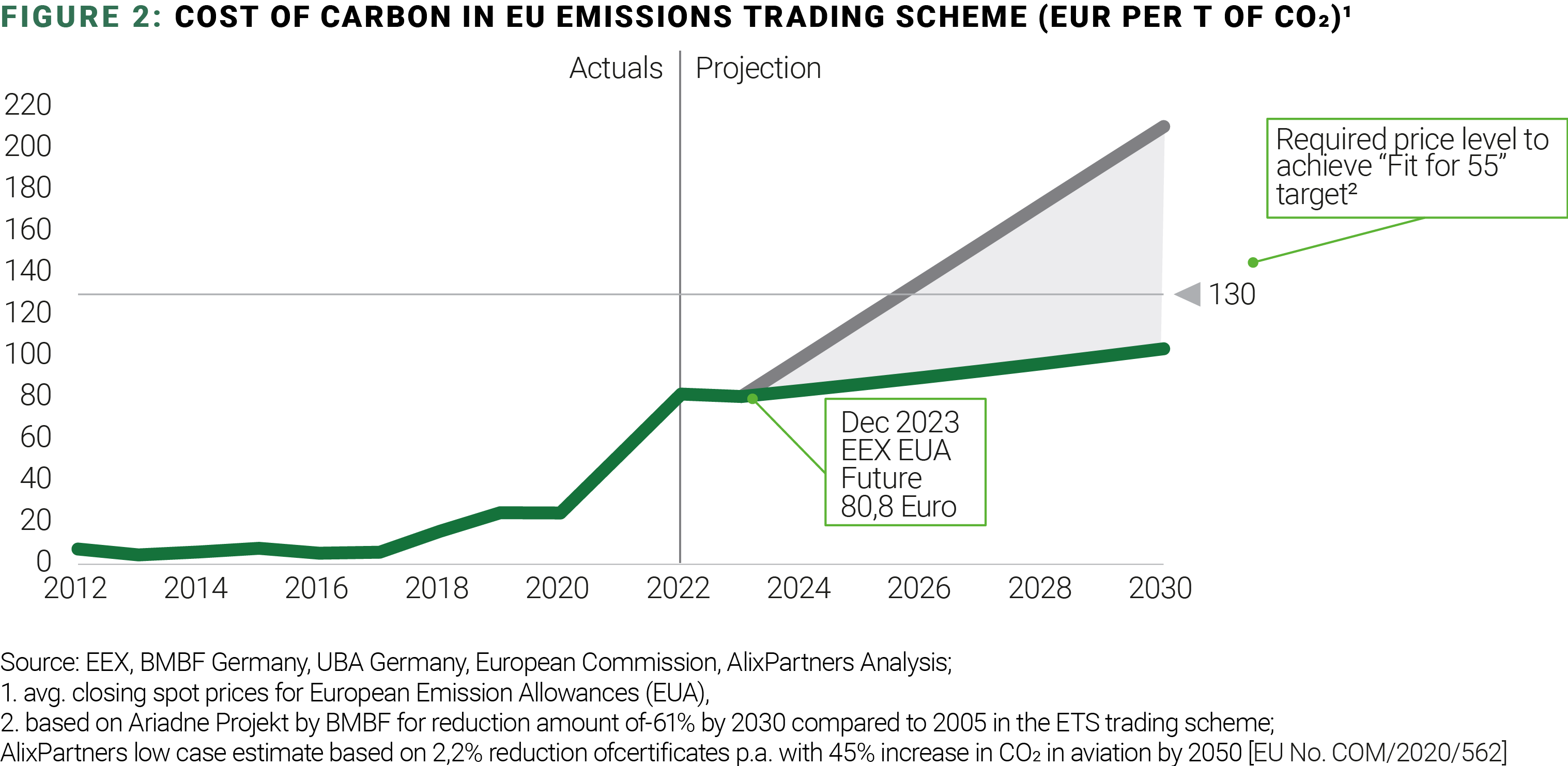
At the same time, investors are shifting money to sustainable assets. The world is attuned to the devastating environmental and social impact that poor ESG performance has on a company's competitiveness, and, in turn, shareholder returns. Institutional investors are increasingly selecting companies willing to set clear ESG targets. The share of total assets under management worldwide devoted to investments billed as sustainable has been increasing in recent years and is expected to grow in the future (see Figure 3). Consequentially, the cost of capital is already higher for companies with poor ESG scores, or an unwillingness to publish their status.
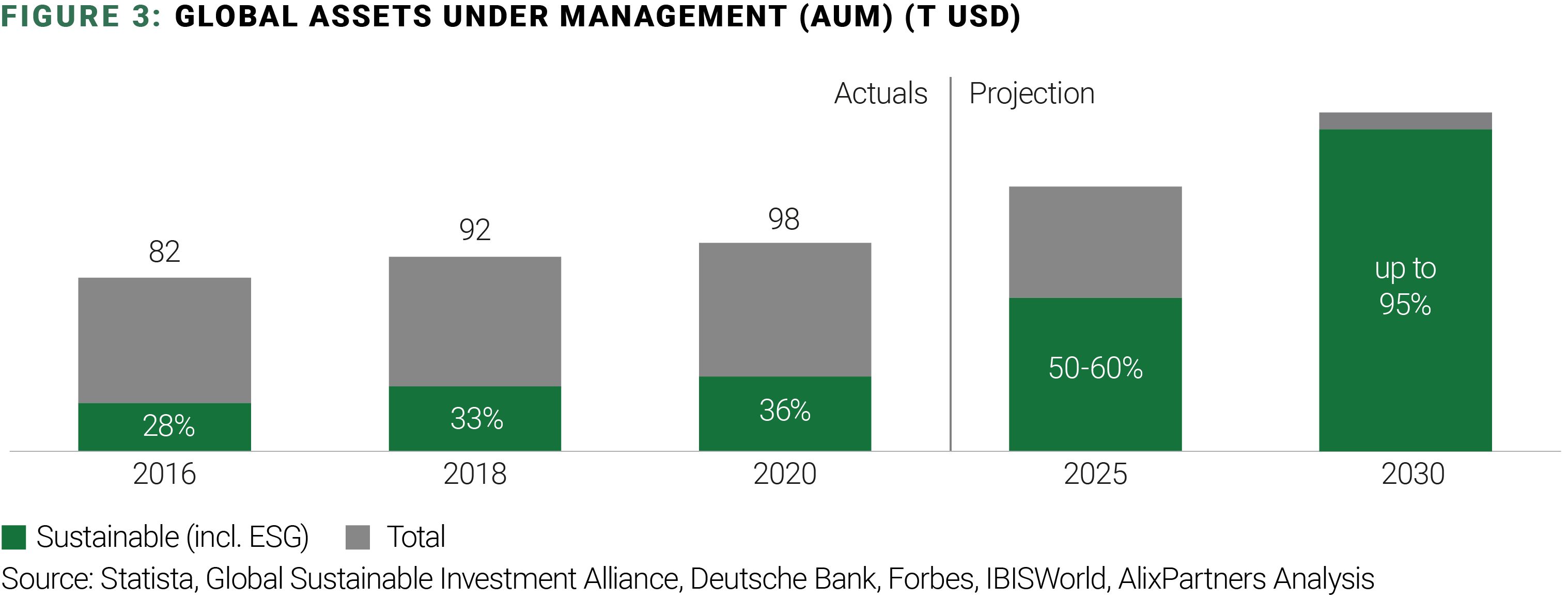
LEVERAGING BUSINESS OPPORTUNITIES AND EXTENDING EXISTING OFFERINGS
Customers are increasingly demanding sustainable products, and this shift is poised to accelerate as climate change's effects become more visible. The scrutiny will get more intense as ESG ratings agencies become more influential and younger employees – who generally expect strong ESG adherence from their employers – compose more of the workforce.
Being an early mover on ESG is a big business opportunity. This isn’t window dressing. Companies acting now can position themselves as leaders, developing cutting edge technologies and creating new business models. Aerospace is a sector where Western companies still have a technological edge e.g., having a deep knowledge, including light-weighting expertise, advanced materials, and hydrogen and battery technology knowhow. One of the most significant and nearest-term opportunities is expanding the existing infrastructure to enable alternatives to Jet A-1 fuel. (With 500 relevant airports, the task is still much easier than converting more than 140,000 petrol stations in the automotive sector.)
The opportunity, however, demands heavy investment and must be supported by governments. The US will subsidize sustainable development via the $370 billion investments dedicated to energy and climate change in the Inflation Reduction Act. Europe now needs to catch up by committing comparable support for the industry to seize business opportunities.
DRIVING CHANGE FROM THE TOP DOWN
Executives need to start by making sure their own house is in order. Defining clear ESG targets and disseminating those targets throughout the entire organization requires a strong framework that includes monitoring the entire supply chain. In building that framework, keep in mind these three considerations that decision-making in aerospace generally follow:
- Product requirements (weight, passenger capacity, safety, cost)
- Product components (airframe, engines, cabin, systems, wings)
- Product lifecycle (development, operation, disposal)
To be effective, ESG principles need to be woven into core product requirements with a clear link to cost so they can be adequately considered in the decision-making process. Considering the cost of carbon for investments and business decisions has been already adopted by some companies, but this can only be the start.
This requires a significant transformation that needs to be driven from the top down, addressing not only the C-Suite but down to operational decision-makers influencing design, manufacturing, procurement, usage, recycling, and other factors.
Aviation is an industry with long development phases and product lifecycles. Therefore, the time is now to act with concrete next steps and an actionable strategy that encompasses a holistic ESG approach with clear targets and roadmap to success.
STANDING STILL IS NOT AN OPTION
Sustainability and ESG are here to stay and will have a significant impact on company’s competitiveness in the future due to:
- future compliance requirements and extensive preparation needed to meet them
- risk of high cost on business operations if ESG is not considered
- clients request for more sustainable products and solutions
- business opportunities to extend product portfolio and service offerings
The entire industry will undergo a substantive shift – are you prepared to lead the way, or will you get caught in an expensive game of catch-up?